As regulations on cultivation facilities begin to take shape, municipalities will continue to investigate power, water, and nutrient use in the industry. The increasingly rigid standards for low-waste facility design require experienced teams, including engineers, contractors and consultants, all working together to ensure efficiency requirements are met. Typically, this involves customized, site-specific equipment, consistently monitoring and providing feedback on all essential inputs and waste. Still, many operation managers and municipalities do not consider the trend towards tighter laws regarding water usage and wastewater discharge. These regulations will impact producers dramatically and may even put some out of business due to higher operating costs and competition.
As the industry evolves, facilities that are already in place must consider new water regulations, which could jeopardize an existing operation’s legality. As drought-prone states like California, Nevada, and Arizona continually develop new laws on cultivation, water volume usage and discharge will be legal issues that municipalities in those states will closely monitor, if they haven’t already.
Incoming Hydroponic Wastewater Regulations
The most common water regulations for cultivation facilities concern volume usage limitations and wastewater disposal procedures. If a facility is regulated on water quality that can be discharged into the sewer, the agricultural runoff water must be processed, made possible with a variety of methods. These methods include:
- Filtration and recycling
- Off-site shipping
- On-site evaporation ponds
- Evaporators
- Dilution
- Processing through artificial wetlands
- Wastewater Treatment
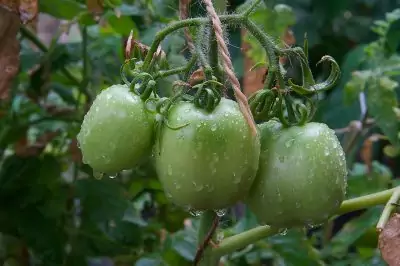
Moving towards Zero Liquid Discharge means moving away from the traditional horticultural method of relying on “drain to waste” systems. The runoff from a drain to waste system is sent literally down the drain into the sewer system, which is a primary concern for regulators. A closed loop system is possible, however input costs would be high compared to a well-engineered, highly efficient drain to waste system. Closed loop systems also require constant water testing and will still produce some form of wastewater discharge, which will need to be processed further.
As an alternative, facilities can be engineered around custom systems that recycle runoff water on a commercial scale. The method of processing run-off water on-site for recycling and volume reduction is currently being used by a variety of industrial facilities. Using reverse osmosis to filter wastewater is the least energy intensive and most economically sustainable way to remove dissolved solids from runoff water, however this application produces concentrated wastewater that must be trucked off-site or evaporated.
Hydroponic Wastewater Management Solutions
If a municipality regulates a facility’s daily water volume usage, that facility must pursue one of the following options:
- Cut back on planned or operational plant production
- Install a recirculating hydroponic system
- Filter and reclaim runoff water for irrigation, or
- Do all three
The potential regulations create an incentive for many cultivators to seek ways to build a facility with “Zero Liquid Discharge” from the start, however, there are many associated challenges with building these types of systems.
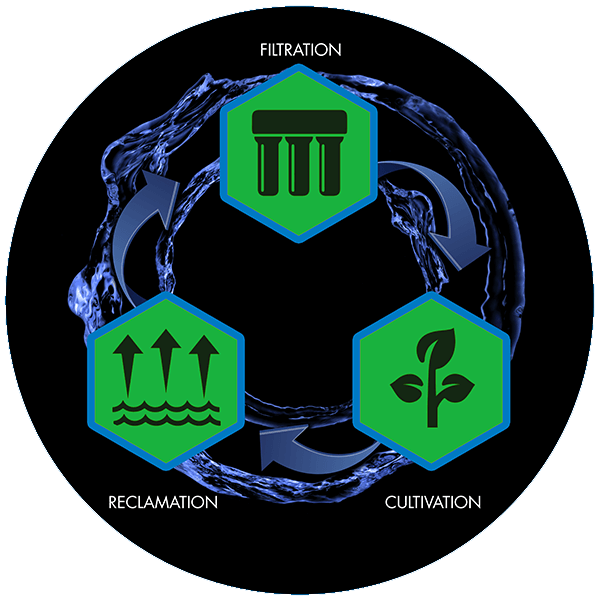
Passing Hydroponic Wastewater Regulations
Since water supply and quality can vary widely across geographic locations, there’s no set standards or consistency with what wastewater disposal regulations municipalities are enforcing on indoor growers. Each municipal water treatment facility’s equipment responds differently, depending on what that municipality’s customers are putting down the drain. Potential grow operations will need to contact their municipality FIRST, to find out what restrictions are in place and how they will affect the permitting process. There is a wide spectrum of what could be required, from needing to treat the wastewater for biological control, balance the pH, or basic sediment filtration, to completely preventing indoor agriculture from ever seeing the light of day by banning any kind of wastewater disposal. This can be the case when high amounts of nitrates, salts, or TDS would be put down the drain, damaging municipal water treatment equipment.
Minimum Liquid Discharge
Facilities dealing with concentrated water discharge regulations usually must truck all nutrient runoff water off-site. Many operations pay for this water to be taken away by the gallon, which can add up quickly due to the large volumes of wastewater needing to be disposed of. However, one way to minimize the liquid discharge of a grow operation is to use reverse osmosis to further concentrate contaminants in wastewater streams so that there’s a smaller volume of wastewater needing to be disposed of, and less frequently trucked off.
The most efficient way to deal with wastewater is to use Commercial Reverse Osmosis to concentrate the contaminants as much as possible, then send the concentrated wastewater to be evaporated or trucked off for safe disposal. This reclaim system is the most economical solution to minimizing wastewater and water usage.
HyperLogic’s Nutrient Runoff Filtration System
Our modular Nutrient Runoff Filtration System can be added to any operation to reclaim the nutrient runoff or final flush water for reuse. Water that would normally be sent down the drain is reclaimed and reused, reducing the total water usage by at least 50% and up to 80%.
Zero Liquid Discharge for Hydroponics
Integrating Commercial Reverse Osmosis and distillation/evaporation is the only way to truly achieve Zero Liquid Discharge, the only downside being high associated costs. These systems are most efficient when treating large volumes of water, which makes them the most suitable option for extremely large commercial/industrial operations. Unless a facility is massive, this means that most grow operations will need to take the approach of saving water by altering growing methods to use as little water as possible, minimizing the volume to be shipped off site for treatment.
HyperLogic works directly with one of the top evaporator companies in the world and can help you get to zero liquid discharge.
Environmentally Conscious Hydroponic Wastewater Solutions—Artificial Wetlands
While all previously mentioned methods are industrial solutions to treating agricultural runoff water, there are a few biological solutions as well. In many cases runoff water can be treated with artificial wetlands. In an artificial wetland, water with dissolved nutrients enters into the system and a variety of bacteria, plants, and other organisms convert the nitrogen-based fertilizers into actual biomass, and in some cases, this means growing a secondary crop. It’s a great solution for any grow operation that has proper permits and land to do this. The problem is that these types of systems are not applicable in an industrial area where the amount of dedicated nearby land needed to make it work isn’t available.
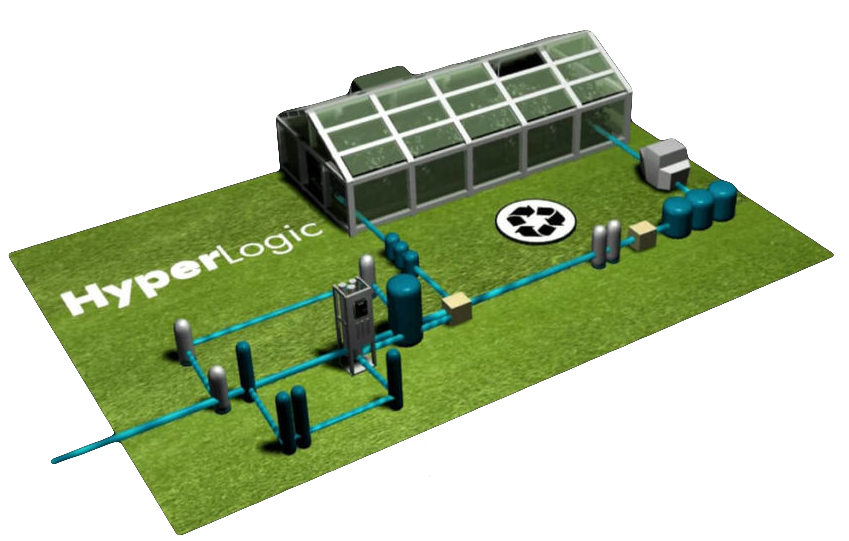
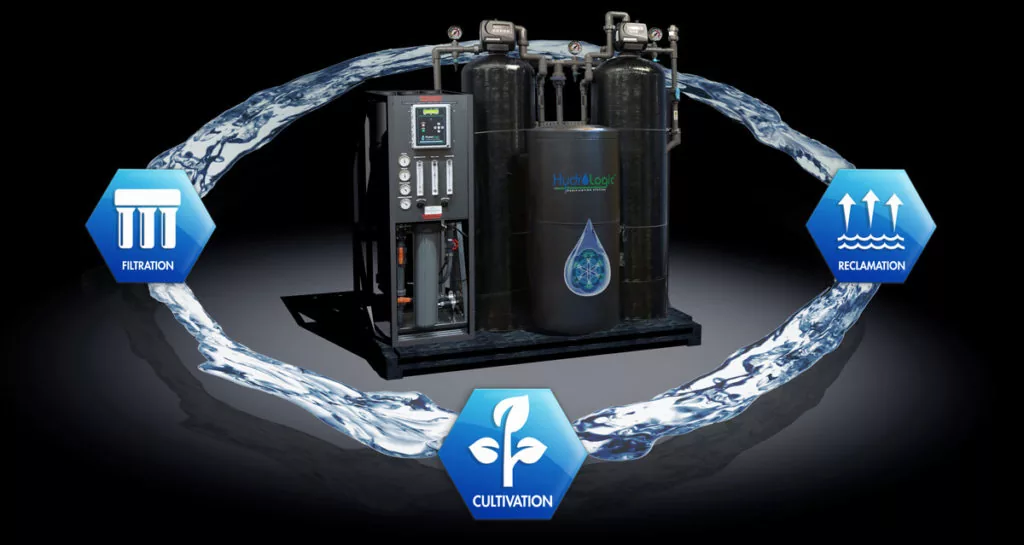